入社5年目で
プロジェクトリーダーに
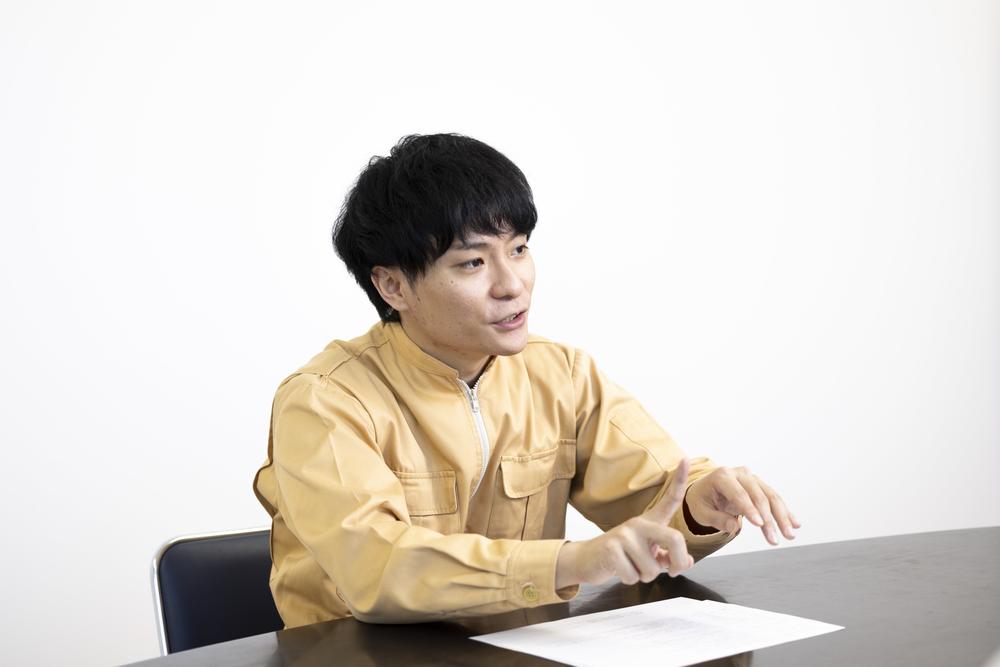
T.F.
私が所属する金型事業本部 金型生産技術部では、生産効率などをより高める、さまざまな改善方法を常に検討しています。
その1つとして、2020年から新たに取り組むことになったのが、生産設備にAMRを導入し、金型の加工や搬送を自動化するプロジェクトです。
AMRとは、工場や倉庫などで、ピッキングや搬送などの作業を自動で行う最新鋭のロボットのことです。床に動線となる磁気テープなどを貼らなくても、搬送ルートをプログラムで算出して移動するため、テープなどが剥がれて誤作動するようなことがなく、設備のレイアウト変更も柔軟に対応できます。
今回のプロジェクトでは、放電によって加工を行うワイヤ放電加工機を用いたラインにロボットを導入。従来は、金型をワイヤ放電加工機にセットして、加工完了後は洗浄機まで運び、洗浄後に保管棚へ戻すという一連の作業を、作業者が手作業で実施していました。加工機へのセットにスキルが必要なため、長年手作業でしたが、これらの作業をアーム(腕)の付いたロボットによって自動化することで、作業者の力量に依存することなく、効率よく加工していくことを考えたのです。
元々このプロジェクトは10名程度のチームで編成され、当時、入社5年目の私がリーダーに抜擢されました。このような未知のプロジェクトを行うのは初めてで、「自分にリーダーが務まるのか……」という不安が大きかったのですが、思い切って引き受けました。
ロボットを使って
国内トップクラスの精度に挑む
T.F.
AMRを使った自動化への取り組みは、当社のどの事業部も取り組んだ実績がなく、参考にできる事例がなかったため、一から考えていく必要がありました。
そこでまず着手したのは、自動化ラインの「あるべき姿」の検討です。さらに投資効果の計算も重要でした。設備を導入することで期待される収入と、運用にかかる支出を細かく検討し、会社として採算が取れるかどうかの確認をしました。
この作業も簡単ではなかったのですが、さらに難しかったのは、国内トップレベルの加工精度が求められたことです。
ワイヤ放電加工機での加工は、マイクロメートル (1/1000mm) 単位の精度が求められます。金型部品をセットする位置が少しでもずれると、高精度な加工ができなくなるため、これまでは手作業で行っていたのです。
また、金型部品は一品一様で、サイズも加工内容も異なる数百種類の部品を扱う必要がありました。通常の自動化は、決まった部品を連続して加工することが多いのですが、私たちは様々な形状の部品に対応できるシステムを構築する必要がありました。
そうした課題を解決するために、加工設備、AMR、治具、洗浄機、システムといったメーカーや商社など、多数の企業と協業しました。通常の設備導入では、ここまで多くの企業とやり取りすることはありませんが、各社と綿密にコミュニケーションを取りながら、少しずつ関係性を構築していきました。
ただ、国内でもまだ事例が少なかった事もあり、メーカーの方にも経験があまりなく、手探りの状態であり想定外のトラブルもたくさん起こりましたが、根気よくトライアンドエラーを繰り返しながら一つずつ課題を解決していきました。
社内でも、製造担当者やシステム担当者からさまざまな意見が出てきたため、その取りまとめに難しさを感じましたが、皆さん協力的な方ばかりで、かつ上司からもサポートがあり、なんとか進めることができました。
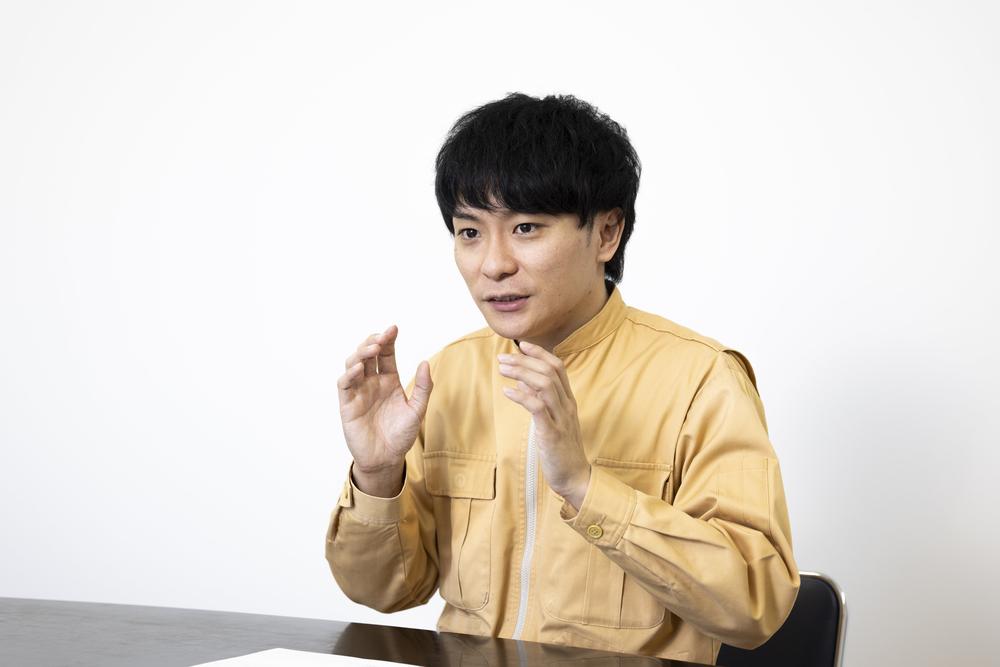
4年がかりで稼働でき
生産性の向上を実現
T.F.
2023年4月に設備を導入し、テスト段階を経て、24年1月から生産ラインでの稼働を開始しました。初めて稼働したときの達成感は、これまで味わったことのないくらいのものでしたが、プロジェクトスタートから4年近くかかってしまい、かつ、小さな不具合が発生したため、自己採点としては、60点ぐらいの出来といった感じでした。ただ、プロジェクトメンバーの皆さんからは「T.F.さんでなければできなかった」と言っていただき、現場の方からもたくさんの労いの言葉を頂きました。
スキルが必要だった工程が、今では少しのサポートで機能するようになり、その結果、熟練の作業者たちは、高度でより創造性が高い業務などに注力することが可能になりました。
また、自動化されたラインは土日も稼働できるため、金曜日にセットすれば、土日のうちに加工作業を終えられます。作業者は休日対応の必要がなくなるので、負担軽減につながりました。
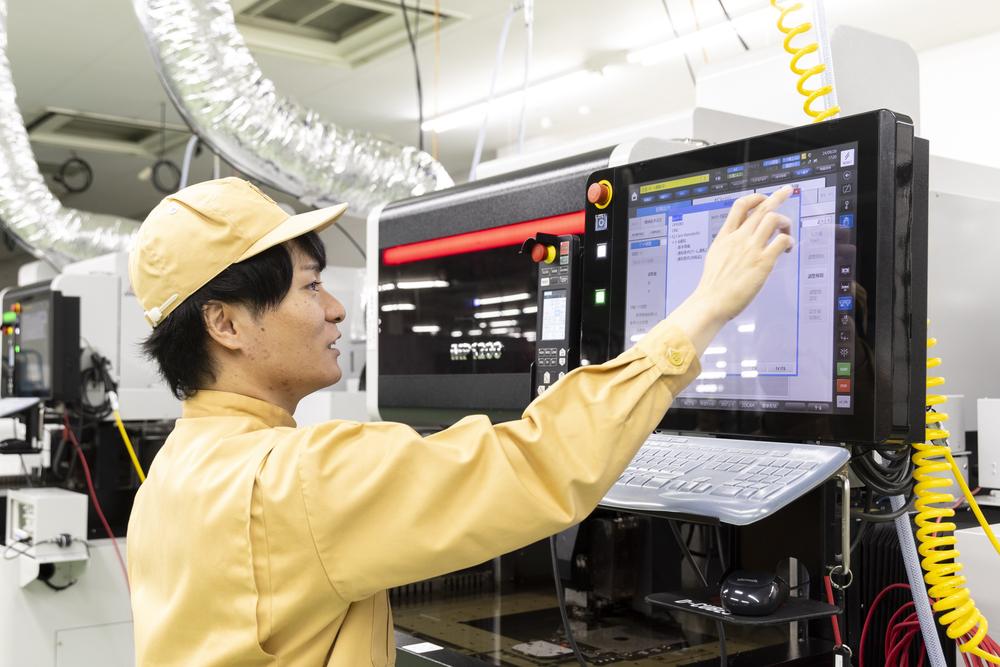
他の生産設備に
AMRを横展開する動きも
T.F.
現在は、まだ数台のワイヤ放電加工機に対応している状況ですが、今後は加工機を増やし、より多くの加工を自動化していく予定です。さらに、今回のAMRの取り組みを、他の生産設備に対しても横展開していこうという動きも出てきています。
また、私の経験や気づきを社内で共有するために、今回の経験で得られた知見をデータとして残していきたいと考えています。例えば、仕様書に書かれた仕様と、完成後の仕様とでは乖離している部分があるので、どのようなプロセスによって乖離が生じたのかをきちんと残しておく予定です。そうすれば、同じ過ちを繰り返さずに済み、横展開もしやすくなると思っています。
今回の経験によって、すべての生産工程を完全に自動化するのは現実的ではないと思うようになりました。金型製造においては、人の知見が必ず求められる工程が存在するからです。今後は、自動化できる作業と、人にしかできない作業を適切にすみ分けながら、効率化を進めていくことが重要だと考えています。
個人的には、プロジェクトに携わったことで、物事を考えるときの視野が広がったと感じています。担当者目線だけでなく、より一段上の視点で考えられるようになりました。また、今年からは新入社員の教育も担当していますが、プロジェクトで得た経験が、業務管理や進捗管理に活きていると実感しています。
今後もさまざまな業務にチャレンジして、新たな視点を見出しながら、会社に貢献していきたいと思っています。
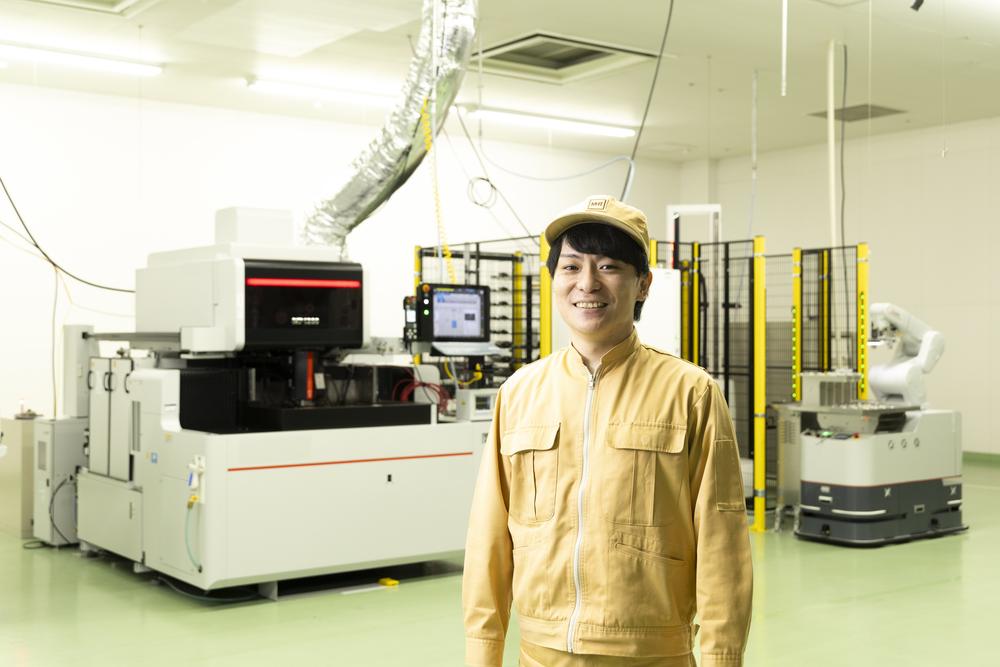