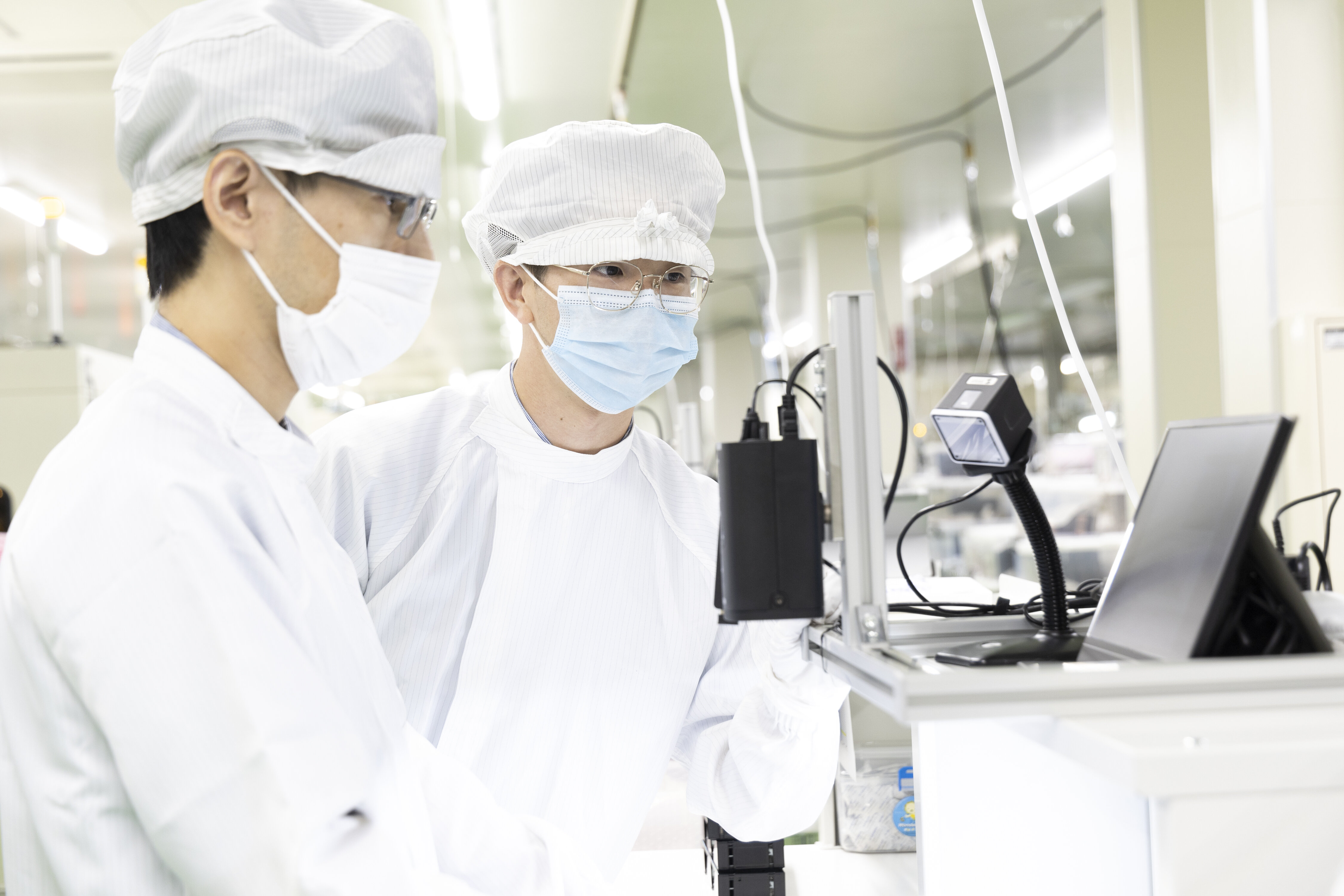
人為的なミスを防ぐための
プロジェクトが始動
S.Y.
私たちが在籍する生産技術グループでは、リードフレームの生産から出荷に至るまでの全作業工程を常に見直し、効率をさらに高めていくための対策を講じています。そのなかで、課題の1つになっていたのが、人為的な「製品の収納間違い」です。
リードフレームは、自動検査装置で検査した後、人の手でケースに収納して出荷します。この時、正しい向きで収納しなければなりませんが、誤って、逆の向きで収納してしまう可能性があったのです。
些細なミスのように見えるかもしれませんが、お客様がそのことに気づかず逆向きで使用してしまうと、設備などの破損へとつながる可能性があるため、そのようなミスは必ず防がなければなりません。
対応策として、複数人によるチェック体制の強化などを行いましたが、その分人手が必要となり、かつ、人為的なミスを100%防ぐことは至難の業です。そこで、人手を使わずにミスを未然に防ぐ方法として考えついたのが、作業支援カメラを使ったシステムです。
同システムは、「リードフレーム」と「作業者の行動」を作業支援カメラで撮影して、画像処理プログラムで正しくケースに収納できているかをチェックし、間違った動作をしていたら警告音が鳴り、次の工程に進めなくなるというものです。
私は、以前働いていた会社で電子機器の製造に携わっていたのですが、そこで作業支援カメラを導入したことがありました。その経験を活かしてカメラを導入すれば、ミスを防げるのではないかと考え、「作業支援カメラ設置プロジェクト」を立ち上げました。
G.T.
私は、途中からこのプロジェクトに参加しました。2017年に新卒で入社してから、製造や技術の仕事を経験した後、マレーシア工場に出向。ちょうど日本に戻り直方事業所に帰任したところで、このプロジェクトがあることを知ったのです。
大学時代に画像処理の研究をした経験があり、現場のめっき工程でも画像処理で検査する機械を使用していたため、少しは知見がありました。そこで、何か貢献できそうだと思い、自ら手を上げプロジェクトに参加したのです。
作業効率が上がるどころか
下がる事態になった……

S.Y.
リードフレームは、幅70㎜、長さ250㎜程度の小さな製品です。その収納ミスを的確に検知するためには、高精度な映像を撮影することが不可欠。そこで、どのカメラを選び、どこに設置していくのか、といった導入前の準備から検討していく必要がありました。複数のカメラを設置すればするほど精度は上がりますが、場所が限られ、クリーンな環境の作業場に、多くの物は設置できないため、1つだけでも鮮明に写すことができるコンパクトなカメラを選定しました。
システムの現場への試験導入は、2022年の夏頃から始めていったのですが、特に難しかったのが、カメラや照明の設置場所です。リードフレームは金属なので、光の入り具合や照明の位置が少しずれるだけで反射してしまいます。反射するとサイズも小さく形状が判別しにくくなるため、ベストな設置場所を探すのに苦労しました。
試行錯誤しながらカメラを設置し、実際に作業を撮影してみたのですが、ここで次の壁にぶつかりました。このシステムを入れることで、作業効率が上がるどころか、悪化してしまったのです。
G.T.
原因は、映像から収納ミスを判定するプログラムにありました。判定する上で、リードフレームの位置情報や照明、画像処理や検査判定といった複数のパラメータを設定する必要があります。多くのパラメータを設定すればするほど検知漏れを防ぐことが可能です。しかしその反面、検知しすぎてしまうため、正しく作業していても警告が鳴り、作業を中断しなければいけないという事態が多発したのです。
S.Y.
正しい作業も止められてしまうので、作業者から見れば困ったシステムです。もともと作業支援カメラで撮影されることは、監視されているような気持ちになりますから、作業者には抵抗感があります。それに拍車をかけてしまいました。
G.T.
収納ミスを判別するために、プログラム上でパラメータを調整する必要がありますが、一筋縄ではいきません。リードフレームは製品によって形状が異なり、1つとして同じ形のものがないからです。
弊社で製造している、膨大な数のリードフレームそれぞれに合わせ最適なパラメータを調整していたら、いくら時間があっても足りません。
数万種類の組み合わせから
最適な組み合わせを探し出す
S.Y.
このままの状態では実用化できませんし、横展開して、ほかの製品の作業チェックに応用することもできません。どうすれば打開できるのか、検討を重ねました。
G.T.
そうして至った結論は、作業の正誤をきちんと判定でき、かつ複数品種のリードフレームに対応できるパラメータの組み合わせを探し出すことでした。
もちろん、簡単なことではありません。先ほども申し上げたように、パラメータは複数あるので、組み合わせると何万種類にも上ります。仮説を立てることである程度絞り込めるとはいえ、どの組み合わせが最適なのか、根気よくトライアンドエラーを繰り返すしかありませんでした。技術室で一人、黙々とプログラムと格闘し、最適なパラメータを探していきました。
その結果、4カ月かけ、7~8割のリードフレームの収納ミスを検知できるパラメータの組み合わせを見つけ出すことができました。
S.Y.
ただ、これはあくまでベースであり、現場で実際に使うためには、製品ごとにパラメータを微調整する必要があります。そのつど、私たちが調整できるわけではありませんので、現場の検査グループの方にパラメータを調整してもらうことになります。
G.T.
パラメータは専門的な話なので、知識がない方はすぐには理解できません。ただでさえネガティブな印象を抱いているのに、面倒な作業まで増えるとなると、導入に対して消極的になってしまいます。
そこで、できる限り簡単に微調整できるようなマニュアルを作成しました。「こういう状況の時は、このパラメータにこういう数字を入力してください」と事細かに記していきました。
私個人の業務と並行して行っていた作業とはいえ、最適なパラメータを探し始めてからマニュアルを完成させるまでに、半年間かかりました。
S.Y.
G.T.の頑張りのおかげで、検知精度が大幅に向上し、作業効率が上がりました。
さらに現場の方たちに使っていただくためには、システムを導入することでポジティブな面があることも説明しました。カメラで映像を残せば、仮に何らかのトラブルがあった時に、自分たちの過失ではないことが証明できる点を特に強調しました。
結果、現場の方にも理解していただくことができ、パラメータの微調整にも快く応じていただけるようになりました。
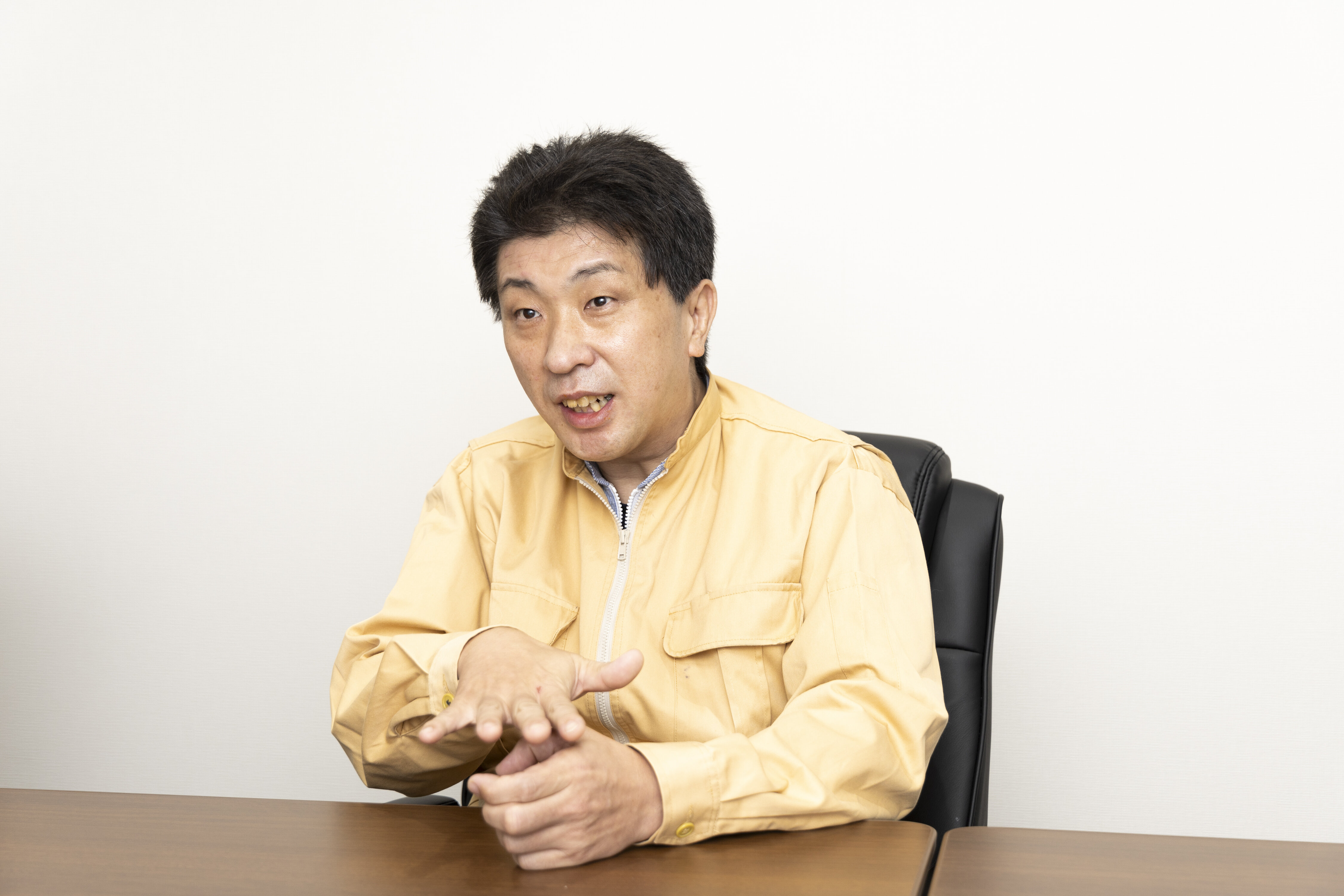
全社的なMESプロジェクトで
この経験を活かす
S.Y.
その後もプログラムの調整を重ねたことで、現在は、リードフレーム全品種のうち、約2割を検知できるようになりました(2024年12月時点)。現状、数十台のカメラが現場で稼働しており、実用化しています。設置後は収納ミスがゼロになり、トラブルの発生を未然に防ぐことができています。
G.T.
正直いって、達成感はまだありません。手つかずの品種が約8割も残っていますし、すでに検知できる品種に関しても、まだまだ完璧ではないと思っています。もっと良くしていかなければならない、という思いが強いですね。
ただ、実用化できたことで、ほかの事業部や工場からも「こちらでも使えないか?」と問い合わせが来るようになりました。横展開することは大変ですが、新たなやりがいを感じています。
S.Y.
作業支援カメラシステムを導入した経験は、現在担当として取り組んでいる、MES(製造実行システム)の導入プロジェクトにも活きてくると感じています。
MESとは、材料の調達から生産までに至る製造プロセスを追跡し、データ化して一元管理するシステムです。これが完成すれば、さまざまなことが自動化されますし、過去の情報から製造プロセスが検証でき、故障などの予防が可能になるため、生産効率が上がります。
G.T.
現在、全社的なプロジェクトとして進められているMESのプロジェクトに私も参加しているのですが、作業支援カメラで行った、「作業データのログを取り、分析して生産に活かす」という経験は、大きなシステムを構築するうえでも活きてくると思っています。
S.Y.
MESの導入の先にあるのは、「スマートファクトリー」の実現です。そこに少しでも貢献できるよう、これからも地道に取り組んでいきたいと考えています。
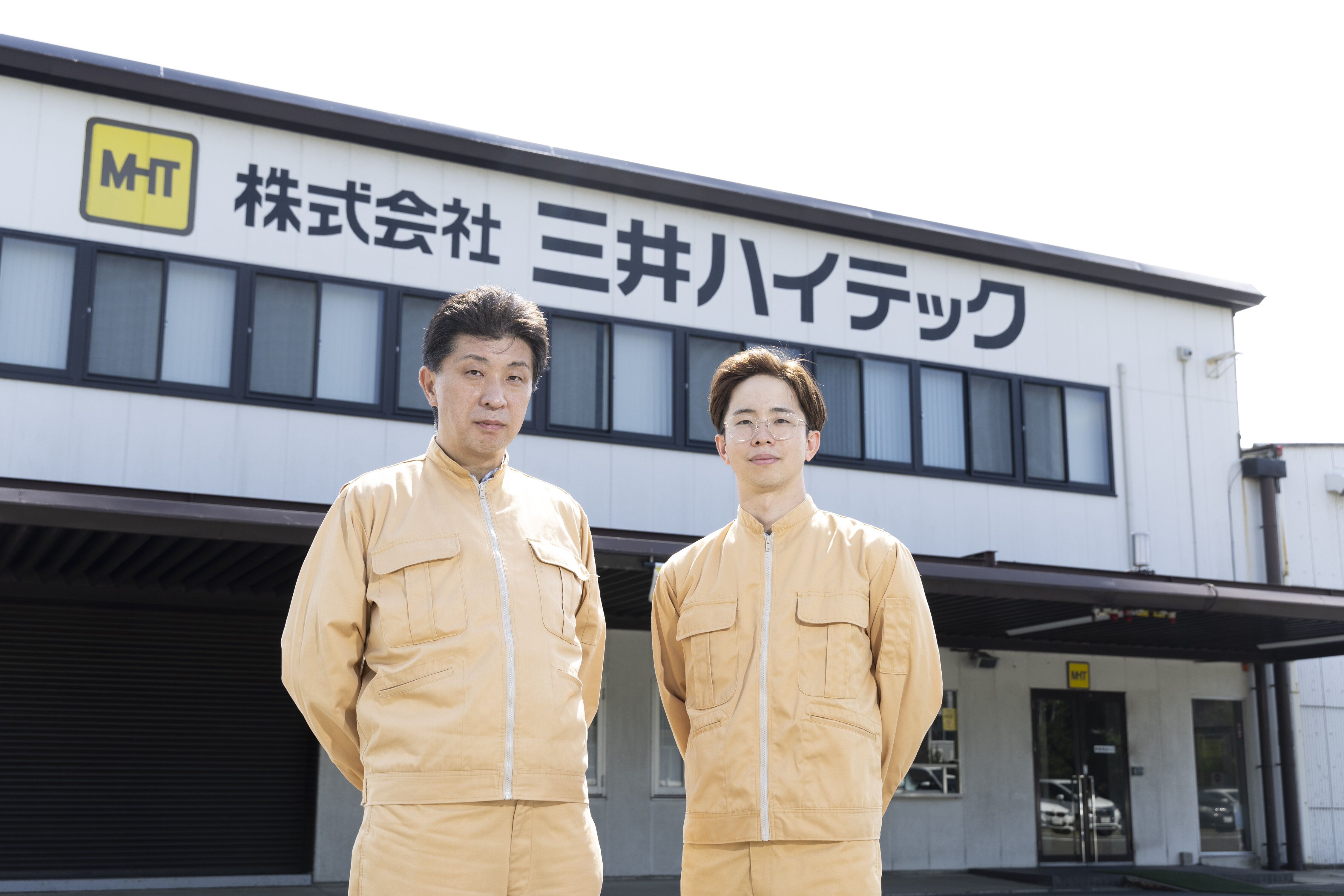